Lean manufacturing offers lots of mental difficulties for all levels in a company. To start with thinking there are wastes in the system is a challenge. People have a safe area. They do not want to leave it. Individuals are really comfy in this territory, whether it is truly good or presumed to be good. Comprehending the reality, there are wastes to be gotten rid of from the system use danger to the safety and security of this convenience area. People consequently are not ready to come out of this, unless they see something they can’t resist. For an instance, individuals will certainly not see their high operation in progress as a waste unless they have a great factor to see it as.
If one can see huge lead time savings and enhanced adaptability as the outcomes of eliminating operate in progression from the system, after that they will have less resistance in looking operate in development as a waste. With all this resistance, lean production is spreading throughout the globe in a rapid stage. This implies the reality that there are numerous, lots of companies comprehend the advantages offered by lean production. This goes to show how solid the lean production principle, as well as concept, is. It has a proven capability of getting rid of the wastes from the system.
The second phase of lean production is recognizing the origin of the wastes. Once you understand the fact that your system has wasted, then it is the moment to eliminate them from the system. This is required for effective lean production implementation. Just how to do this? Firstly, we need to understand the series in which wastes to be gotten rid of. Priority needs to remain in eliminating huge wastes which have the most significant effect on the system and more. When this is done, we will have to comprehend the root causes of this issue. We will certainly have to map this origin, as well as systematically eliminate them. We can make use of a lean production device like the Ishikawa layout or a cause and effect diagram is doing.
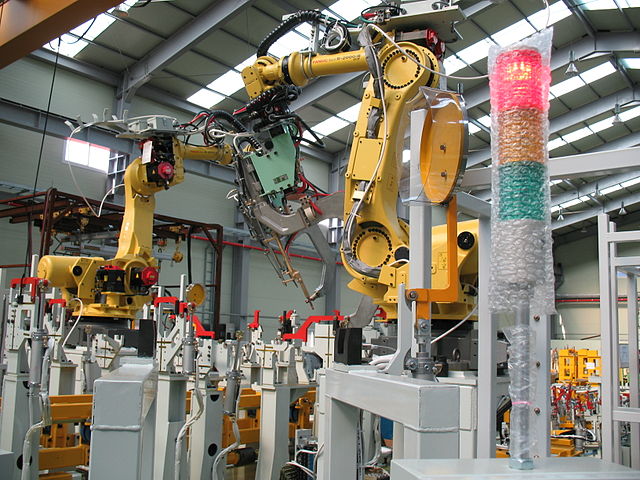
When we understand the root causes, it is the moment to get rid of these root causes from the system. Actually, this can be referred to as the starting factor of the lean production implementation procedure. This process needs a lot of skill, leadership, and also assistance. Speaking to the feelings of individuals is among the vital elements of this phase. For example, if you have found out that equipment breakdown is the prime resource of the problem, then you will need to collaborate with the inefficiencies of the maintenance process. This will certainly create stress among the people in the upkeep department if they are not educated well to recognize the lean production principle. These scenarios should be taken care of with wonderful treatment.
At the end of the process of eliminating these sources, it is extremely important to ensure that you have efficiently eliminated the waste. Removing 90% will certainly refrain. Once you see to it that you have actually efficiently removed the determined waste, afterward you can repeat the exact same cycle for additional trouble. This will continue. Problems will be recognized continually as well as will certainly be removed continually.
To learn more about precision waterjet cutting, visit their page for more info.